Improve Customer Satisfaction
Deliver product faster and document repairs and overhauls more fully.
Increase Job Profitability
Rapid customer interaction & adaptive processes mean more jobs finished in the same time.
Reduce Errors
MRO/RMA manufacturing operators supported by adaptive instructions perform tasks faster & more reliably.
Expedite, Simplify and Control the Full Lifecycle of Your Products
Increase Business Opportunities
Improve Customer Satisfaction
Eliminate Inefficiencies
Reduce Material Costs
Reduce Liability Exposure
Increase Visibility & Control
Some other clients we’ve helped
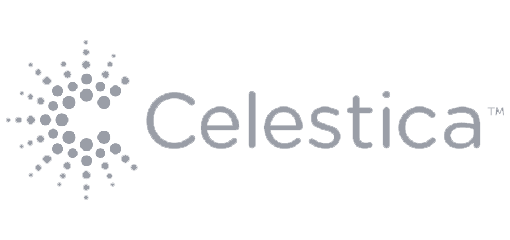
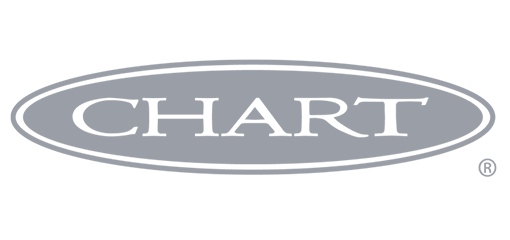
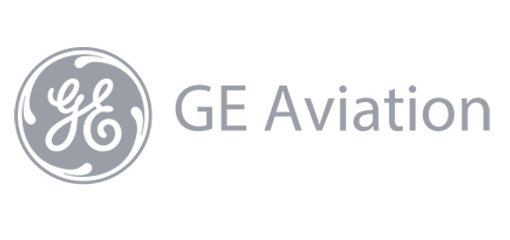
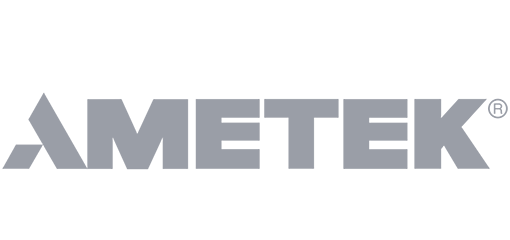
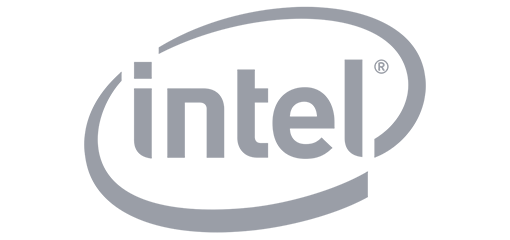