Materials Assurance
Eliminate material related issues in the materials management process without the need for bloated buffer stock.
Quality Assurance
Eliminate material-handling related defects.
Performance Assurance
Maximize flexibility and reduce material-related loss time with an automated materials management system designed for supply chain operations.
Satisfy Both Internal Operational Targets, As Well As Providing Confidence And Satisfaction For The Customer
Improve Quality & Reliability
Complete Material Traceability
Facilitate Compliance & Conformance
Accelerate Response Time
Optimize Factory Utilization
Boost Customer Confidence
Some other clients we’ve helped
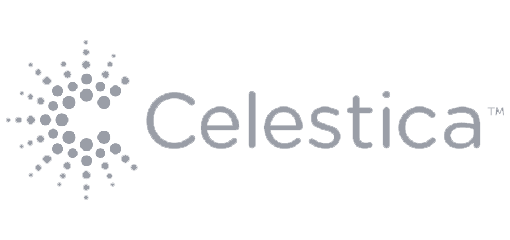
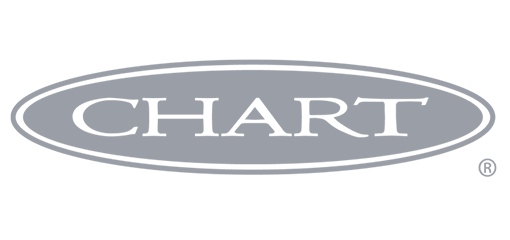
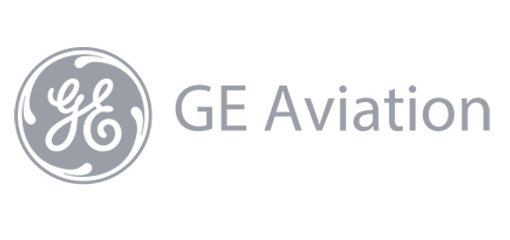
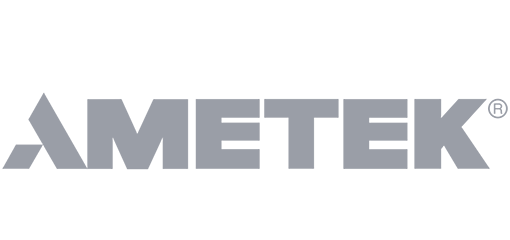
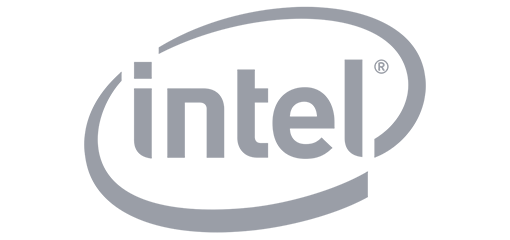